Echolot
- Blindfischer
- Beiträge: 538
- Registriert: 5. Okt 2011, 06:51
- Mein Kayak: Wilderness Tarpon 120, Hobie Outback
- Kayak-Pate: Ja
- Wohnort: Reinfeld
- Alter: 59
Dez 2011
02
07:14
Das ist manchmal einfach so, hatte ich auch schon, da löst sich der Geber dann plötzlich nach einer Weile wieder, keine Ahnung woran das liegt( vielleicht auch Luftfeuchtigkeit/Temperatur?)
Dann muß man das nochmal machen und dann ist gut.
Beim Quadra Geber wär ich auch eher skeptisch mit den Seitenecho´s, ich glaube das geht besser wenn man eine Stelle hat, wo der Rumpf aufgekielt ist, an einer flachen Stelle gehen die Seitenstrahlen doch ins Rumpf-Nirwana oder?
Gruß
Dirk
Dann muß man das nochmal machen und dann ist gut.
Beim Quadra Geber wär ich auch eher skeptisch mit den Seitenecho´s, ich glaube das geht besser wenn man eine Stelle hat, wo der Rumpf aufgekielt ist, an einer flachen Stelle gehen die Seitenstrahlen doch ins Rumpf-Nirwana oder?
Gruß
Dirk
- vatas-sohn
- Beiträge: 13418
- Registriert: 4. Okt 2011, 16:38
- Mein Kayak: Hobie Mirage Outback 2016 Hobie Pro Angler 12 2014
- Kayak-Pate: Nein
- Wohnort: 14776 Brandenburg an der Havel
- Alter: 60
Dez 2011
02
08:00
Genau deshalb meine Frage danach, wo Kulti es versucht hat. Ich denke auch, daß man so einen Bereich besonders ins Auge fassen sollte. Zudem sollte der Bereich möglichst nicht von den Wirbeln der Flossen mit Luftblasen versorgt werden. Also habe ich mich für den vorderen Kielbereich entschieden- etwa 70 cm vom Bug entfernt. Weiterer Vorteil: Man kommt sehr gut ran....Blindfischer hat geschrieben:...Beim Quadra Geber wär ich auch eher skeptisch mit den Seitenecho´s, ich glaube das geht besser wenn man eine Stelle hat, wo der Rumpf aufgekielt ist, an einer flachen Stelle gehen die Seitenstrahlen doch ins Rumpf-Nirwana oder?...
Aber gerade bin ich noch auf der Suche nach dem richtigen Silikon


Grüße!
Ron
"Wenn der Mensch so viel Vernunft hätte wie Verstand, wäre vieles einfacher." (Linus Pauling)

Ron
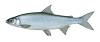
- vatas-sohn
- Beiträge: 13418
- Registriert: 4. Okt 2011, 16:38
- Mein Kayak: Hobie Mirage Outback 2016 Hobie Pro Angler 12 2014
- Kayak-Pate: Nein
- Wohnort: 14776 Brandenburg an der Havel
- Alter: 60
Dez 2011
03
12:51
So, Antwort von Wcker-Chemie (weltweit größter Hersteller von Silikonen) ist da:
Sehr geehrter Herr Lühnsdorf,
...Wenngleich wir Sie bitten, noch zu klären was unter NV zu verstehen ist, wollen wir Ihnen unser RTV-2 Produkt ELASTOSIL RT 601 A/B vorschlagen. Es ist additionsvernetzed, transparent, dünnflüssig in der Verarbeitung und hat eine Shore A Härte 45. Höhere Shore A Härten sind nicht mehr "transparent" verfügbar. Wir haben das technische Datenblatt sowie die Verarbeitungshinweise für additionsvernetzende Siliconkautschuke beigefügt.
...Mit freundlichen Grüßen
Ulrike Weber
Zur Erklärung:
Silikone haben wie andere Materialien auch besondere Spezifikationen. Die wichtigsten für unsere Zwecke sind:
- RTV (Raumtemperaturvernetzend)
- NV (Niedrigviskos- d.h. gut bis sehr gut fließfähig im Rohzustand)
- additionsvernetzend (d.h. zwei Komponenten werden nach genauen Vorgaben gemischt und addieren sich zu einem Produkt- deshalb ist genaues Arbeiten zwingend notwendig!)
- Shore-A als Angabe der Härte des fertigen Vulkanisats (je Höher dieser Wert, desto besser leitet das Silikon die Schallwellen= geringerer Signalverlust)
- transparent (nicht zwingend notwendig, aber am besten, da z.B. die Pigmente (bei schwarz: s.g. Rußschwarz) Störungen verursachen können.)
Zur Verarbeitung:
Die zwei Komponenten werden sorgsam abgewogen und in einem Gefäß, welches die vierfache Menge als die Mischung aufnehmen kann, sanft vermischt. Jetzt kommt der etwas schwierige Teil der Prozedur: das s.g. Evakuieren. Dabei wird in dem Gefäß ein Vakuum erzeugt, daß dafür sorgt, daß die Luftblasen entweichen können. Da sich dabei die Mischung bis zu knapp dem Vierfachen ausdehnen kann, muß das Gefäß so groß sein. Anschließend wird zunächst der Bootsboden und der Geber vorsichtig etwas damit eingestrichen. Anschließend wird das Silikon in einem dünnen Strahl blasenfrei eingegossen. Die Masse vulkanisiert gleichmäßig durch den gesamten Gußkörper ohne jeden Schrumpf je nach Typ in 30 bis 60 min. komplett durch. Sofort danach ist das Boot einsatzbereit. Das Ergebnis ist ein transparentes, sehr gut Schallwellen leitendes und vor Allem luftblasenfreies Bett für den Geber. Also die optimale Lösung.
Klar kann man auch mit Baumarktsilikon gute Ergebnisse erzielen, aber an die Qualität dieser Ausführung wird das nie heranreichen. Dafür hat das Silikon aus dem Baumarkt andere Vorzüge, die nicht von der Hand zu weisen sind:
- sehr preiswert (etwa 1/10 des 2K-Systems)
- sehr leicht und mit geringem Aufwand zu verarbeiten
- befriedigendes Ergebnis
- der Formbau, bzw. die Abschottung eines Gußbereiches entfällt
Aber es hat auch Nachteile:
- große Gefahr von Lufteinschlüssen
- geringe Shore-A Werte der Silikone
- kondensationsvernetzend (das Silikon vernetzt von außen nach innen und benötigt dafür je nach Schichtstärke sehr lange)
- geringere Haltbarkeit
So, nun kann jeder selbst entscheiden, für welche Variante er sich entscheidet. Meine Entscheidung ist eindeutig zu Gunsten des 2K Systems gefallen.....
Sehr geehrter Herr Lühnsdorf,
...Wenngleich wir Sie bitten, noch zu klären was unter NV zu verstehen ist, wollen wir Ihnen unser RTV-2 Produkt ELASTOSIL RT 601 A/B vorschlagen. Es ist additionsvernetzed, transparent, dünnflüssig in der Verarbeitung und hat eine Shore A Härte 45. Höhere Shore A Härten sind nicht mehr "transparent" verfügbar. Wir haben das technische Datenblatt sowie die Verarbeitungshinweise für additionsvernetzende Siliconkautschuke beigefügt.
...Mit freundlichen Grüßen
Ulrike Weber
Zur Erklärung:
Silikone haben wie andere Materialien auch besondere Spezifikationen. Die wichtigsten für unsere Zwecke sind:
- RTV (Raumtemperaturvernetzend)
- NV (Niedrigviskos- d.h. gut bis sehr gut fließfähig im Rohzustand)
- additionsvernetzend (d.h. zwei Komponenten werden nach genauen Vorgaben gemischt und addieren sich zu einem Produkt- deshalb ist genaues Arbeiten zwingend notwendig!)
- Shore-A als Angabe der Härte des fertigen Vulkanisats (je Höher dieser Wert, desto besser leitet das Silikon die Schallwellen= geringerer Signalverlust)
- transparent (nicht zwingend notwendig, aber am besten, da z.B. die Pigmente (bei schwarz: s.g. Rußschwarz) Störungen verursachen können.)
Zur Verarbeitung:
Die zwei Komponenten werden sorgsam abgewogen und in einem Gefäß, welches die vierfache Menge als die Mischung aufnehmen kann, sanft vermischt. Jetzt kommt der etwas schwierige Teil der Prozedur: das s.g. Evakuieren. Dabei wird in dem Gefäß ein Vakuum erzeugt, daß dafür sorgt, daß die Luftblasen entweichen können. Da sich dabei die Mischung bis zu knapp dem Vierfachen ausdehnen kann, muß das Gefäß so groß sein. Anschließend wird zunächst der Bootsboden und der Geber vorsichtig etwas damit eingestrichen. Anschließend wird das Silikon in einem dünnen Strahl blasenfrei eingegossen. Die Masse vulkanisiert gleichmäßig durch den gesamten Gußkörper ohne jeden Schrumpf je nach Typ in 30 bis 60 min. komplett durch. Sofort danach ist das Boot einsatzbereit. Das Ergebnis ist ein transparentes, sehr gut Schallwellen leitendes und vor Allem luftblasenfreies Bett für den Geber. Also die optimale Lösung.
Klar kann man auch mit Baumarktsilikon gute Ergebnisse erzielen, aber an die Qualität dieser Ausführung wird das nie heranreichen. Dafür hat das Silikon aus dem Baumarkt andere Vorzüge, die nicht von der Hand zu weisen sind:
- sehr preiswert (etwa 1/10 des 2K-Systems)
- sehr leicht und mit geringem Aufwand zu verarbeiten
- befriedigendes Ergebnis
- der Formbau, bzw. die Abschottung eines Gußbereiches entfällt
Aber es hat auch Nachteile:
- große Gefahr von Lufteinschlüssen
- geringe Shore-A Werte der Silikone
- kondensationsvernetzend (das Silikon vernetzt von außen nach innen und benötigt dafür je nach Schichtstärke sehr lange)
- geringere Haltbarkeit
So, nun kann jeder selbst entscheiden, für welche Variante er sich entscheidet. Meine Entscheidung ist eindeutig zu Gunsten des 2K Systems gefallen.....

Grüße!
Ron
"Wenn der Mensch so viel Vernunft hätte wie Verstand, wäre vieles einfacher." (Linus Pauling)

Ron
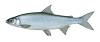
Dez 2011
14
20:54
DJTMichel hat geschrieben:vielleicht war mein Silikon zu alt, ich habe vor dem Verkleben gründlich mit Aceton entfettet, auch den Geber
Von der Benutzung von Azeton kann ich nur dringend abraten

Also Finger weg von Aceton und Co. sonst geht das Yak vorzeitig in die ewigen Jagdgründe


I wish I was fishing !
RTM K-Largo
RTM K-Largo
- vatas-sohn
- Beiträge: 13418
- Registriert: 4. Okt 2011, 16:38
- Mein Kayak: Hobie Mirage Outback 2016 Hobie Pro Angler 12 2014
- Kayak-Pate: Nein
- Wohnort: 14776 Brandenburg an der Havel
- Alter: 60
Dez 2011
15
00:40
Oneway 71 hat geschrieben:DJTMichel hat geschrieben:vielleicht war mein Silikon zu alt, ich habe vor dem Verkleben gründlich mit Aceton entfettet, auch den Geber
Von der Benutzung von Azeton kann ich nur dringend abratenMacht zwar prima "Fettfrei" ( was im Rumpf aber eher nicht vorhanden sein sollte), zieht aber auch super die Weichmacher aus dem Yakmaterial (idr. PE oder PP). Das führt zu vorzeitiger Versprödung !!! (später also Löcher !!!)
Also Finger weg von Aceton und Co. sonst geht das Yak vorzeitig in die ewigen Jagdgründe![]()
Mhhh....ich bin etwas ratlos!


Weiterhin sehe ich keine Möglichkeit, mit Aceton oder ähnlichen Lösungsmittteln PP oder PE zu schädigen. Wenn das ginge, dann hätte man eine prima Möglichkeit gefunden um die besagten Materialien anzulösen und somit zu verkleben. Und das ist ja bekanntlich echt schwierig!
Aber ich lerne gerne dazu! Drum interessiert mich, wo Du das her hast! Wäre für die Info sehr dankbar!
Grüße!
Ron
"Wenn der Mensch so viel Vernunft hätte wie Verstand, wäre vieles einfacher." (Linus Pauling)

Ron
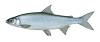
- liwu72
- Beiträge: 290
- Registriert: 8. Dez 2011, 14:59
- Mein Kayak: Manta Ray 14 + Slayer 13 Propel
- Kayak-Pate: Nein
- Kontaktdaten:
Dez 2011
15
22:48
vatas-sohn hat geschrieben:
Weiterhin sehe ich keine Möglichkeit, mit Aceton oder ähnlichen Lösungsmittteln PP oder PE zu schädigen. Wenn das ginge, dann hätte man eine prima Möglichkeit gefunden um die besagten Materialien anzulösen und somit zu verkleben. Und das ist ja bekanntlich echt schwierig!
Aber ich lerne gerne dazu! Drum interessiert mich, wo Du das her hast! Wäre für die Info sehr dankbar!
hm... ich bin zwar kein Chemiker, aber es gibt Klebstoffe mit denen das durchaus möglich ist. Ich hab zwar noch nix an mein Kajak geklebt aber dafür musste ich mal bei meinem Wäschetrockner den Griff wieder ankleben. Es gibt tatsächlich Klebstoffe die speziell dafür gemacht sind. Muss mal schauen ob ich davon noch was im Keller hab. Wenn ich das Zeug finde dann schreib ich das mal hier rein. Ich weiß nur noch das ich die oberfläche fettfrei machen musste, dann kam ein Lösungsmittel drauf und dann der Klebstoff. Die Klebung hält heute noch nach zwei Jahren bombennfest. Auf jeden Fall war es ein spezieller Kunststoffkleber kein Sekundenkleber oder son Zeug. Auf denen steht ja meistens drauf klebt kein PE oder ähnliches.
Der Griff unterscheidet sicher aber sicher in der Art Kunststoff zum dem aus dem Kajaks gemacht werden.
Dez 2011
18
21:33
vatas-sohn hat geschrieben:Oneway 71 hat geschrieben:DJTMichel hat geschrieben:vielleicht war mein Silikon zu alt, ich habe vor dem Verkleben gründlich mit Aceton entfettet, auch den Geber
Mhhh....ich bin etwas ratlos!Mich würde mal interessieren, woher Du das mit den Weichmachern, die man mit Lösungsmitteln aus dem PE oder PP bekommt hast?
Soweit ich weiß, wird PE oder PP u.A. gerade deswegen für Bootskörper genutzt, weil es durch seine langkettigen Moleküle naturgemäß eine gewisse Elastizität aufweist. Nach meinem Kenntnisstand wird den Materialien entweder ~1,5 bis 5% TPE (Thermoplastisches Elastomer) zugesetzt, oder sie werden im Prozess coploymerisiert, d.h. ein s.g. Weichmacher wird in das Molekül eingefügt- ist also unlösbar (Zerstörung ausgenommen) mit diesem verbunden, was dazu führt, daß das Material auch bei niedrigeren Temperaturen rel. elastisch ist und bleibt......Und auf Oberflächen nur aufgebrachte Weichmacher (s.g. Äußere oder kovalente Weichmachung) interessieren in diesem Bereich sowieso nicht.
Weiterhin sehe ich keine Möglichkeit, mit Aceton oder ähnlichen Lösungsmittteln PP oder PE zu schädigen. Wenn das ginge, dann hätte man eine prima Möglichkeit gefunden um die besagten Materialien anzulösen und somit zu verkleben. Und das ist ja bekanntlich echt schwierig!
Aber ich lerne gerne dazu! Drum interessiert mich, wo Du das her hast! Wäre für die Info sehr dankbar!
Ob PP oder PE gerade im Bootsbau verwendet werden, weil sie "eine gewisse Elastizität aufweisen", kann ich nicht sagen. Ich dachte das liegt eher daran, dass sich diese Polyolefine prima blasen und tiefziehen lassen (Herstellverfahren unserer PE-Yaks). PP ist da schon weniger geeignet, da es bei Temperaturen von kleiner /gleich 0°C versprödet, brechen kann. Ich bleibe also mal beim PE, bei dem es aber auch verschiedene Typen gibt. Die Unterschiede liegen im wesentlichen in der Länge der Polymerketten, welche sogar stark verzweigt /vernetzt sein können. Dadurch ergeben sich dann Änderungen in der Dichte und die Materialeigenschaften ändern sich. Je höher die Dichte, desto besser sind die mechanische und chemische Beständigkeit. Es werden sogar Tanks aus PE gebaut , in denen Aceton gelagert und transportiert werden. Warum sollte dann also was passieren, wenn mit Aceton gereinigt / entfettet wird?
Ich habe hier lediglich den Finger gehoben und eine Warnung ausgesprochen, weil ich NICHT weiß, welcher Art "unser" Yak- PE ist. Ich vermute mal ,das es eher die langkettige HD-PE Variante ist. Wie auch immer, mir ging es um die enthaltenen Weichmacher (WM). Bei der PE Herstellung werden einige Zusatzstoffe beigefügt, Füllstoffe (z.B. Kreide),WM (es gibt verschiedene Typen), Farbpigmente,.... Menge und Art regeln wo und wie(viel) an den Molekülketten angelagert wird. Eine Materialeigenschaft von PE ist die Durchlässigkeit von Sauerstoff, Kohlendioxid und Aromen (das hat NICHTS mit Anlösen der Oberfläche zu tun) Areomen sind z.B. Ketone, hier ist die einfachste Form das ACETON. Und beim Durchwandern des PE werden eben auch Weichmacher herausgelöst ( die aber auch einer "schleichenden Wanderung "unterliegen), da eben nicht stabil im Thermoplast angelagert bzw. im Überschuß zugeschlagen werden.Eine Materialschädigung findet also statt.
Das ganze Thema kenne ich im übrigen aus meinem Beruf (u.a. IM Chemie), wobei es da aber eher um Verarbeitung von PVC und TPO (thermoplastisches Polyolefin) in KFZ Innenräumen geht.
Kurzum , es muß beim Einsatz von Aceton nichts passieren, kann aber. Sofort sieht man eh nichts ! Das tückische ist nur, dass das Resultat erst viel später (mglw. Jahrzehnte) auftritt. Dann kann man sich aber eh mal ein neues Yak gönnen, oder ?:P
Im übrigen auch niemals Instrumententafeln, Türverkleidungen, Sitze eures Autos mit Alkohol (z.B.Glasreiniger) reinigen (sofern aus PVC, TPO, Kunstleder (ist auch PVC ). Hier findet die Versprödung wesentlich schneller statt ! Und solche "Reklamationen am Material" sehe ich fast jede Woche. Unser Labor kann die Ursache aber Prima lokalisieren (WM Entzug durch Alkohol )

Bestre Grüße, Jörg
I wish I was fishing !
RTM K-Largo
RTM K-Largo
- Blindfischer
- Beiträge: 538
- Registriert: 5. Okt 2011, 06:51
- Mein Kayak: Wilderness Tarpon 120, Hobie Outback
- Kayak-Pate: Ja
- Wohnort: Reinfeld
- Alter: 59
Dez 2011
19
07:49
Soweit ich weiß, sind 90% der SOT´s im Rotomould Verfahren aud HDPE hergestellt, Blasen oder Tiefziehen wird nur von wenigen Herstellern praktiziert.
Bei Rotomould kommt das PE Granulat in die Form und diese wird dann im Ofen unter ständiger Bewegung erwärmt. Dadurch schmilzt das Granulat und verteilt sich gleichmäßig in der Form.
Dann nur noch abkühlen lassen, Form auf und das Boot ist fast fertig.
Aber das Thema Weichmacher im Material und Langzeitverhalten ist mal spannend zu klären, mal sehen ob ich was genaueres herausbekomme.
Gruß
Dirk
Bei Rotomould kommt das PE Granulat in die Form und diese wird dann im Ofen unter ständiger Bewegung erwärmt. Dadurch schmilzt das Granulat und verteilt sich gleichmäßig in der Form.
Dann nur noch abkühlen lassen, Form auf und das Boot ist fast fertig.
Aber das Thema Weichmacher im Material und Langzeitverhalten ist mal spannend zu klären, mal sehen ob ich was genaueres herausbekomme.
Gruß
Dirk
Dez 2011
24
14:10
Darüber war vor ca. halbem Jahr mal ein interessanter Bericht im Fernsehen. Kajaks werden wirklich fast alle im "Rotationsverfahren" hergestellt, sprich sie werden "geschleudert"! Führt auch dazu, dass der flüssige Kunststoff durch die Fliehkräfte verdichtet wird und das Material eine höhere Festigkeit erhält!Blindfischer hat geschrieben: Soweit ich weiß, sind 90% der SOT´s im Rotomould Verfahren aud HDPE hergestellt, Blasen oder Tiefziehen wird nur von wenigen Herstellern praktiziert.
Bei Rotomould kommt das PE Granulat in die Form und diese wird dann im Ofen unter ständiger Bewegung erwärmt. Dadurch schmilzt das Granulat und verteilt sich gleichmäßig in der Form.
Dann nur noch abkühlen lassen, Form auf und das Boot ist fast fertig.